How We Stopped Scale Build-Up in Boiler Tubes with Pulsafeeder Chem-Tech XP Series Peristaltic Metering Pumps
The Challenge
The Customer was using a solenoid-activated diaphragm metering pump to inject an anti-scaling chemical into their boiler. The Company that supplied the pump and monitored the water reported high quantities of scale regardless of the amount of anti-scaling solution they used.
The problem was that the check valves on the head of the pump were clogging and causing the pump to lose its prime and ability to provide a suction lift of the chemical out of its container. This in-turn prevented the proper amount of antiscalant from being injected into the boiler water. Without enough of an antiscalant dose in the water, significant amounts of scale began to build up over time within the boiler. This scale & rust build up decreased the boiler’s efficiency and increased the companies operating and maintenance costs and had a potential to become a dangerous situation had the scale began to plug some of the boiler tubes.
Why is scale build-up a big problem in boiler tubes?
Any scale build-up in boiler tubes narrows the pipe diameter and decreases the proper flow of water throughout the boiler. There can’t be an optimal heat transfer with a reduced flow, which leads to lower heating efficiency and fuel wastage and could, if left unchecked, create a dangerous situation should the tubes become clogged entirely.
For example, a scale build-up of as little as 4.3 mm causes around a 20% decrease in efficiency and inflates the operating costs of the boiler.
The Solution
Our application expert—Joe Marotta—talked with the customer about their pump issues and offered up peristaltic pumps as a solution. Joe recommended a peristaltic pump because of its seal-less design and its ability to operate without check valves in the pump head: Why this type of pump: the valves can’t clog up if there aren’t any valves! A peristaltic pump, like the Pulsafeeder Chem-Tech XP model that was recommended in this case, comes with a very low maintenance cost because it only has one tube, which a serviceperson can change out very quickly and easily. The pump also has the added benefits of dry-run capabilities and is, of course, self-priming.
The Result
With the pump managing to tackle each of the customer’s pain points, the results were remarkable, including:
- Optimal chemical injection
- Reduced service & maintenance costs associated with the boiler
- Reduced downtime
- Increased boiler efficiency & energy savings
- Improved safety
In terms of the customers return-on-investment (ROI), if we just only consider the cost of a maintenance person coming in to unclog or replace valves every month at around $100 – $150 per hour, then, based on the price of the new pump, they saw a positive ROI in under 10 months. When factoring in the other benefits, such as fuels savings and better boiler efficiency, the ROI is in fact much quicker.
Technology Used
We used Pulsafeeder Chem-Tech XP Series Peristaltic Metering Pump to solve the customer’s problems.
Pulsafeeder Chem-Tech XP Series Specs:
- Flow: 4 – 80 GPD (0.60 to 12.6 LPH),
- Pressure: 125 PSI (8.6 bar)
- Turn Down: 20:1
- Viscosity: 300 cps
- Inherently Degassing
- Self-Priming
- Pulse Input
- Flow Switch Activated
- 7 Day/8 Event Electronic Timer
- Chemical Resistant Materials
How The Peristaltic Metering Pump Works
- A rotating shoe passes along the length of the hose, creating a seal between the suction and discharge side of the pump.
- As the rotor turns, the sealing pressure moves along the tube and pushes the product into the discharge line.
- When the pressure releases, the hose recovers, creating a vacuum that draws the product into the suction side.
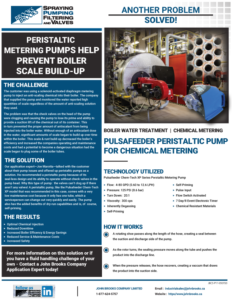
Join our Mailing List
Resources
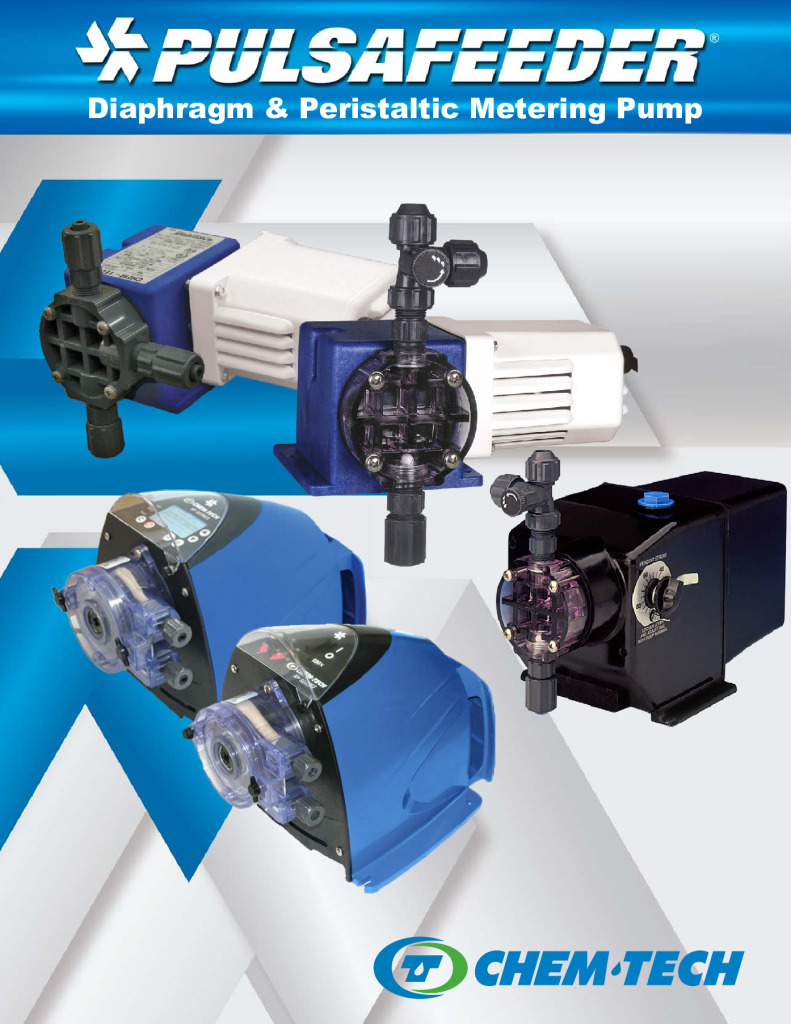
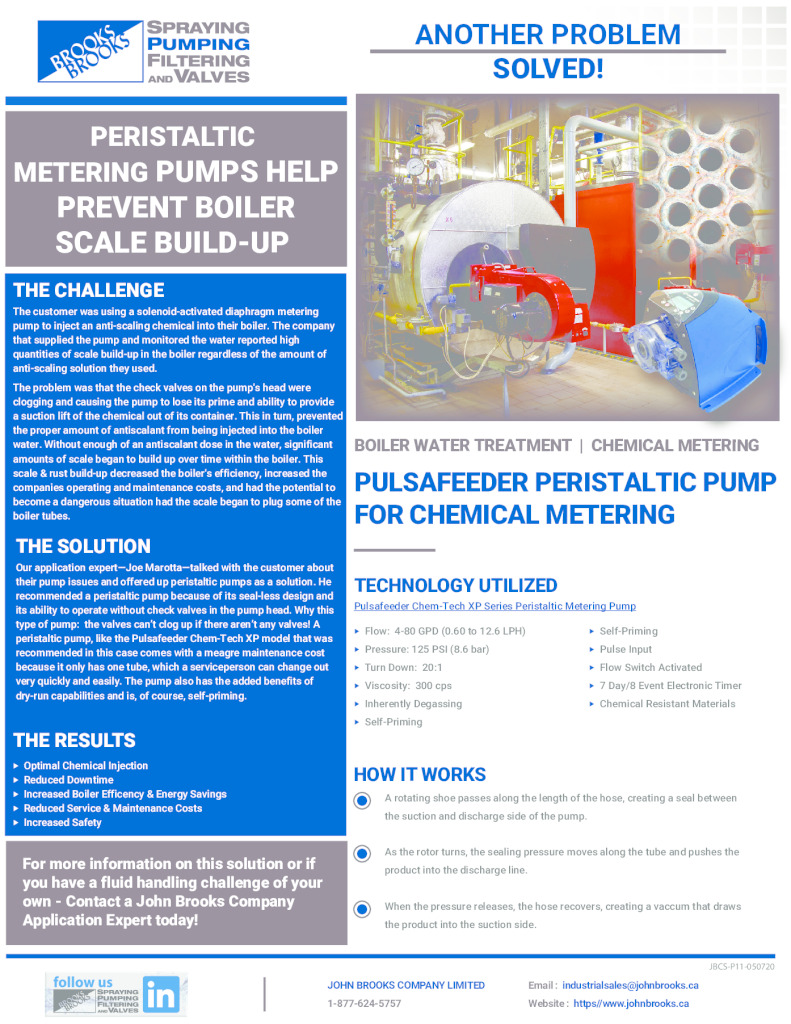
Case Study: Improve Boiler Efficiency and Reduce Maintenance Downtime with Pulsafeeder Peristaltic Metering Pumps
DownloadSize: 2 MB
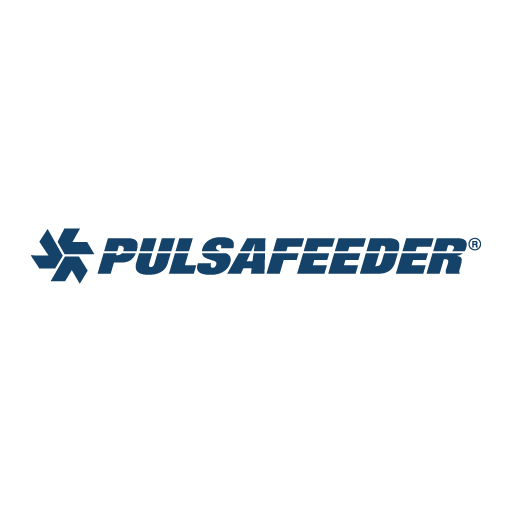
See All Products from Pulsafeeder SPO